Complete guide to rotomolding: processes, benefits, and applications
09 de April de 2024 - Polyethylene, Rotomolding
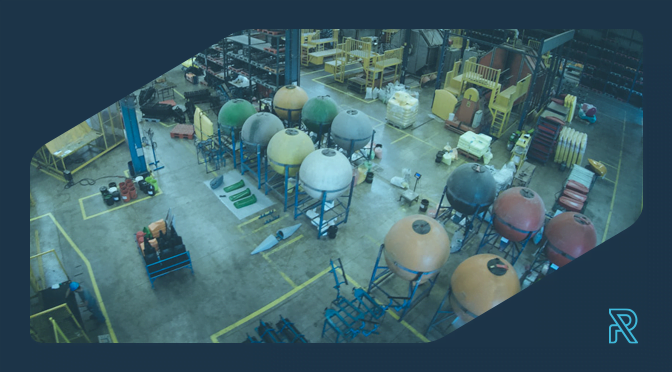
In recent years, industries from various sectors have witnessed a revolution in how parts are made: rotomolding.
More than just an innovative and highly efficient manufacturing technique, this process has become a fundamental pillar in several industries and companies, shaping the landscape of national production in remarkable ways, as explained by the website plástico.com.br.
Today, we’ll take a deeper dive into the world of rotomolding, from its basic principles to its most advanced applications, highlighting its potential to drive growth and innovation across many businesses.
Keep reading to learn more!
What is rotomolding?
Also known as rotational casting or rotational molding, this method is used to produce hollow parts in a variety of sizes, shapes, and dimensions.
Rotomolding companies have stood out not only for their versatility, but also for their ability to deliver customized, high-quality solutions tailored to the specific demands of each sector.
In Brazil, where the pursuit of efficiency and innovation is constant, these companies have found fertile ground to grow, becoming essential tools for organizations looking to stay competitive in a constantly evolving market.
How are rotomolded parts developed?
The rotomolding process requires a careful combination of materials, temperature, and movement to create robust, high-quality products. It involves the following steps:
Preparation: Everything starts with the mold, which can be made of metal or plastic. This item, generally hollow and shaped like the desired final part, is meticulously prepared to receive the thermoplastic material.
Rotation and Heating: With the mold properly prepared, the heating process begins. Polyethylene is introduced into the mold, which is then rotated along multiple axes inside an oven. This rotational movement is essential as it ensures the uniform distribution of material along all the mold walls, preventing defects or imperfections in the final part.
Solidification and Cooling: After the heating and rotation period, the mold is gradually cooled. This controlled cooling is crucial to ensure that the material solidifies properly, maintaining its shape and mechanical properties. Cooling too quickly can lead to warping or residual stress, compromising the quality of the part.
Demolding and Finishing: Once the material has fully solidified, the part is carefully removed from the mold. Depending on the part’s complexity and finishing requirements, additional processes may be needed—such as cutting, polishing, or painting—to ensure that the final rotomolded products meet the required quality standards.
Benefits of rotomolding for companies
Talking about rotomolding means talking about a world of advantages for companies that choose to invest in this technology. Among the benefits of rotomolding that directly impact the corporate routine, we can highlight:
Low Production Cost: Compared to other manufacturing methods such as injection or blo molding, rotomolded plastic offers excellent cost-effectiveness. This is partly due to the simplicity of the process, which requires fewer machines and less specialized labor. Moreover, it enables the production of complex parts in a single step, eliminating the need for additional assembly processes, saving both time and resources.
Design Flexibility: The possibilities here are virtually limitless, allowing the creation of parts with complex shapes and details. This is possible thanks to the versatile nature of the process, which supports the use of flexible molds and the incorporation of features such as ribs, reinforcements, and built-in fittings directly into the part.
Waste Reduction: Since rotomolding uses only the exact amount of material needed to fill the mold, it results in less waste compared to other manufacturing techniques. In addition, the thermoplastic material used in rotomolding is often recyclable, which contributes to reducing environmental impact and adopting more sustainable practices within companies.
Long Product Lifespan: Rotomolded parts are produced to be durable and resistant, capable of withstanding harsh usage conditions while maintaining their mechanical properties over time. This results in products with a significantly longer lifespan compared to those manufactured using other methods, which translates into long-term savings for companies and greater customer satisfaction.
Main applications of rotomolding
Given its many advantages, it is no surprise that numerous sectors use rotomolding in their daily operations. Let’s explore some of the main applications of this versatile process and how it has been essential in meeting the specific needs of different market segments:
Automotive: Used in the manufacturing of fuel tanks, bumpers, door panels, center consoles, and other internal and external vehicle components.
Agricultural: Applied in the production of agrochemical and seed containers, water tanks, irrigation equipment, and other solutions for storing and transporting agricultural inputs.
Industrial Packaging: Essential for the manufacturing of containers, drums, pallets, and other resistant and durable storage units.
Leisure and Recreation: Kayaks, stand-up paddleboards, toys, portable pools, and other equipment are also made using this technique.
Urban Furniture: Used in the production of benches, trash bins, bicycle baskets, light posts, and other elements of public furniture.
With rotomolding, your company goes the extra mile
There is no doubt that rotomolding is the answer for industries seeking efficiency, cost-effectiveness, and versatility. More than just meeting your sector’s specific needs, this process brings numerous lasting benefits that take your company to a new level of competitiveness and prepare it for the ever- changing demands of the modern market.
The solutions you’re looking for are at Rotoplastyc
Now that you’re familiar with the economic and technical benefits of rotomolding, it’s clear that this method is essential for developing innovative, high-quality products.
That’s why, at Rotoplastyc, we understand your business needs and manufacture custom rotomolded parts that match your demands. Get in touch with us and find out how we can help improve your company’s efficiency.