Enhanced manufacturing capacity: Rotoplastyc’s differentials in rotomolding
19 de September de 2023 - Events, Polyethylene, Rotomolding
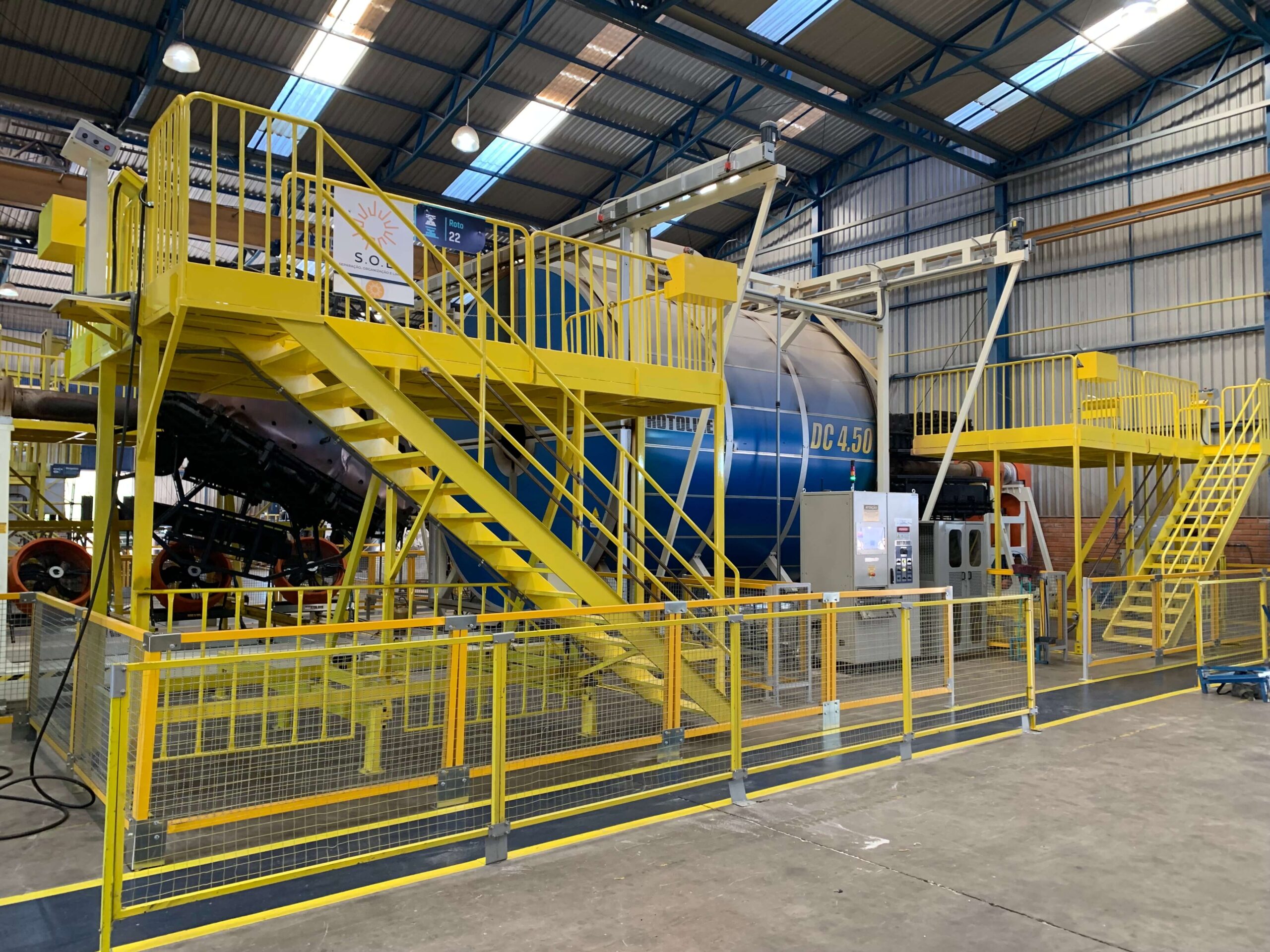
Discover how Rotoplastyc’s investments are boosting production capacity with advanced technology and automation.
In our ongoing pursuit of excellence, innovation, and meeting market demands, Rotoplastyc continuously invests in improving its processes and production capacity. Over the last 18 months, these investments have intensified, from acquiring new rotomolding machines to upgrading manufacturing facilities.
Innovation and Efficiency in Production To meet growing market demand, investments have totaled over BRL 8 million in the past 18 months, including the addition of a new production line and two rotomolding machines. “We increased our installed capacity by 30% with the acquisition of the equipment: a Carousel with a 3,600 mm diameter oven capacity and a Shuttle with a 4,500 mm diameter capacity”, explains Jeferson Nagorny, Industrial Manager at Rotoplastyc. The Carousel is so named because it has independent carts that move the arms through the five stages of the process, allowing for sequential high-volume production. The Shuttle features a central oven, two cooling stations, and two straight and/or offset arms, enabling the production of different products and the use of multiple molds simultaneously—each with unique cycles and recipes.
Improvements in manufacturing facilities
The demand for large-scale production requires machines that can keep up. However, production efficiency also depends on having facilities tailored to that demand and a work environment that supports employees’ well-being.
“In addition to investing in machinery, we also improved our manufacturing facilities by purchasing 15 air coolers and revitalizing the plant, providing greater comfort for our employees. We expanded and optimized the assembly and finishing areas, implementing finishing lines based on the LEAN concept (Lean manufacturing or lean production is a management philosophy derived from the Toyota Production System, which focuses on waste reduction)”, explains the manager. Furthermore, we implemented the MES (Manufacturing Execution System) system across all our machines to track OEE (Overall Equipment Effectiveness) and enable automatic data logging, thus boosting productivity and inventory accuracy. “We established visual management for mold storage and created new storage areas to support our expanding product portfolio. All these efforts combined result in greater quality and production efficiency”, adds Jeferson.
Building the Future of
Industry
Organizational culture plays a key role in the evolution of industry. That’s why, at Rotoplastyc, efforts in this area are made every day. “We’re working hard to improve our organizational culture through programs like SOL, based on 5S principles, and Minifactory (ShopFloor), which applies performance monitoring at the gemba (a LEAN management practice that brings factory floor and leadership closer). With this, we’re able to promote employee and leadership engagement so that everyone can reach higher levels of performance”, he concludes.
Ready to Shape the Future of Your Business?
Rotoplastyc currently serves national and multinational companies with custom polyethylene rotomolded technical parts. Contact us to learn more about our customized solutions and advanced industrial production technology. Let’s shape the future of your business together!
Request your quote with us: https://rotoplastyc.com.br/oem/