Mold investment for rotomolding offers excellent cost-benefit
15 de December de 2022 - Polyethylene, Products, Rotomolding
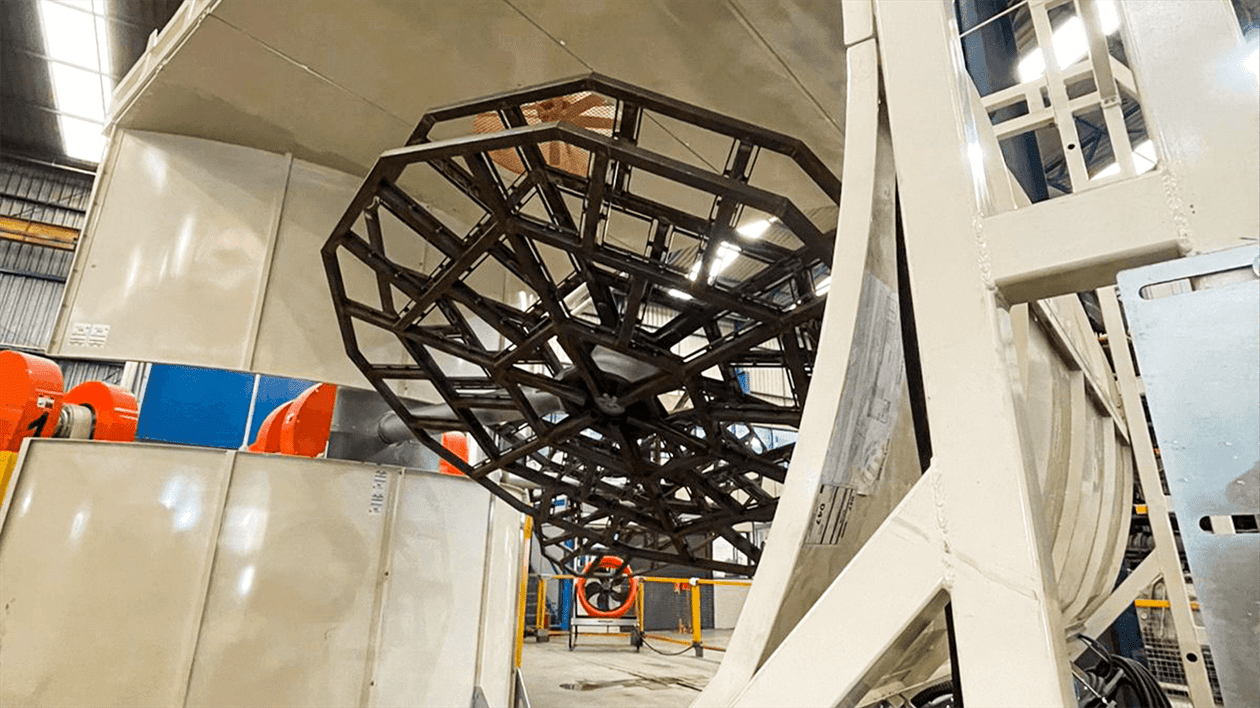
Compared to other industrial processes, rotomolding can produce large-scale parts with a relatively low investment in tooling, making molds for rotomolding an excellent cost-effective option.
If your company is planning to develop a part to be manufactured in rotomolded polyethylene, now is the time to produce the mold. Concerned about the required investment? You should know that molds (or matrices) in rotomolding have a significantly better cost-benefit ratio than those used in other industrial processes, and they are often more affordable.
It is the mold that allows for the development of complex parts in any shape—lighter, smoother, seamless, and with a flawless finish. When opting for a rotomolded part, if the business owner is unsure about investing in a mold, they can calculate: will the profit from selling the part or machine cover the mold investment within a set number of months or years? Will the mold continue producing parts for another set number of years?
The answers will almost certainly be yes. You can also consider the materials used in mold production. The most common for rotomolding are carbon steel, stainless steel, and aluminum.
It is important to remember that rotomolding—also known as rotational molding—is widely used in the industrial sector. This plastic transformation process uses rotomolded polyethylene to create more durable parts with a long service life. The rotomolding process involves transforming plastic polymers into hollow parts, allowing the production of lightweight components with excellent cost-effectiveness.
Moldmaking
Rotoplastyc has an in-house moldmaking department where it designs and manufactures molds for rotomolded parts according to the specific needs of each project. The department is fully equipped, featuring engineering, modeling, moldmaking, and a quality laboratory, and it offers the following services: PPAP (Production Part Approva Process), FMEA (Failure Mode and Effects Analysis), APQP (Advanced Product Quality Planning), and MASP (Method of Analysis for Solving Problems).
Now that you understand the cost-effectiveness of moldmaking for outsourcing rotomolded parts, learn more about the importance of design in the development of new products by visiting the link.