Learn more about Rotoplastyc Quality
22 de February de 2022 - Institutional, Rotomolding
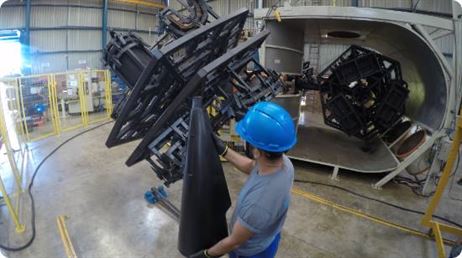
At Rotoplastyc, we strive for excellence in product quality, actively overseeing every stage, from raw material acquisition to development, manufacturing, and product release. All procedures are designed within our quality management system to increase process and product efficiency and enhance customer satisfaction.
Below are some of the defined and implemented processes that aim to meet our customers’ requirements effectively:
● Inspections: A process conducted to assess the compliance of products and operations. The main types of inspections carried out at Rotoplastyc include:
○ Receiving inspection;
○ In-process inspection during rotomolding;
○ Inspection during finishing;
○ Intermediate and final inspection.
● Development of New or Modified Items: This process evaluates all new or altered products to confirm their compliance with design specifications or customer requirements before beginning supply.
● Calibration and Verification of Instruments: This process controls the calibration and verification of measurement and monitoring instruments used to ensure the reliability and accuracy of our production processes.
● Non-Conformance Handling: A process for identifying, segregating, recording, and addressing non-conforming internal products and customer complaints.
● Warranty and Technical Support: A process that outlines how to address non-conformities and corrective actions in cases of product failure in the field.
● Tooling Control: A process that verifies and monitors the use of devices employed in the manufacturing and inspection of the products produced.
● Supplier Performance Evaluation: A process for evaluating the performance of suppliers of raw materials used in the manufacturing of the product. This process involves compiling data related to product quality and delivery time.
To ensure product quality, several tools are used, such as PPAP, APQP, FMEA, and MASP, among others.
● PPAP – Production Part Approval Process: Determines whether all engineering design records and specification requirements are properly understood by the company, and whether the manufacturing process has the potential to produce products that consistently meet these requirements during a production run.
● APQP – Advanced Product Quality Planning: A structured method to define and establish the necessary steps to ensure a product meets customer expectations.
● FMEA – Failure Mode and Effects Analysis: A tool used to prevent potential issue during manufacturing processes.
● MASP – Method of Analysis for Solving Problems: A quality management methodology focused on identifying and solving problems.
The use of these tools results in higher-quality products as they enable continuous improvement efforts. For example: waste reduction; production optimization; improved product quality; lower rejection and rework rates; fewer customer complaints and service calls; reduced cost of poor quality; increased customer satisfaction; enhanced reliability of Rotoplastyc’s products; and access to new markets.
All manufactured parts undergo inspections, during which items are audited according to their inspection plans. The defined and executed processes aim to fully meet customer expectations and cover the following areas:
● Visual Inspections: Assessment of the aesthetic quality of parts and verification of components (e.g., rivets, inserts, etc.) by trained personnel using specialized equipment such as borescopes, which are used for internal tank inspections.
● Dimensional Measurement: Precision tools such as calipers, rulers, squares, coordinate measuring arms, height gauges, and others are used.
● Thickness Measurement: Using an Ultrasonic Thickness Gauge, critical areas of the parts are inspected to ensure they are within the tolerances defined in the technical drawing.
● Sealing Tests: These are the main tests performed on tanks, aiming to detect potential leaks.
● Fuel Sensor Tests: Tests carried out on level sensors installed in fuel tanks to ensure they meet the specifications defined by engineering/client, using multimeter test benches for readings.
● Granulometry and Dry Flow Tests: Conducted on micronized polyethylene to verify the compliance of the micronization process.
Rotoplastyc has been ISO 9001 certified since 2007, providing the company with methodologies to organize its processes, which in turn enhances the quality of the service or product delivered to the customer.